FSSC22000
(食品安全システム認証)
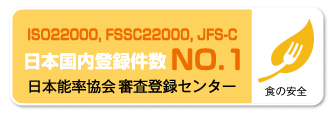
審査実績NO.1の審査期間だから安心!
審査および
認証取得支援サポート
CASE.8
連載:効果的な運用事例 日世株式会社 様 [FSSC22000]
顧客の要請、新工場内部統制強化のためFSSC22000を導入
~ 技術の伝承とクレーム低減にデジタルメディアを活用
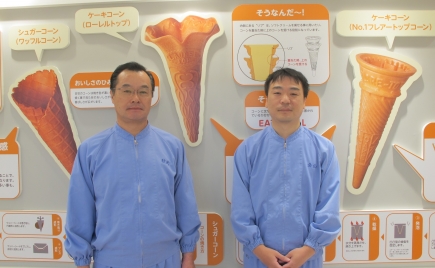
取材先:日世株式会社
コーン生産部部長 東松山工場長 秋武 幸博 様(左)
コーン生産部 管理グループ 品質管理課 課長補佐 金山 洋平 様(右)
日世様はソフトクリームのNo.1リーディングカンパニー。ソフトクリーム商品を総合プロデュースしています。ソフトクリームではいろいろな味が楽しめるミックスをはじめとしたオリジナル商品を送り出し、ソフトクリームを作るフリーザーでは新しい技術と考え方を搭載した機器を開発するなど、今日のソフトクリーム人気に大いに貢献しています。
2015年、日世様は、コーンカップの生産拠点である東京工場と枚方工場を集約し、埼玉県東松山市に新たに東松山工場を建設しました。同工場は、年間12億個以上のコーンカップ生産能力を擁する、国内最大規模のコーンカップ工場です。
FSSC22000の認証については、2014年に当時のコーンカップ製造拠点のひとつ、枚方工場で取得し、2017年に東松山工場への工場移転統合が完了する際に移しています。その東松山工場では、FSSC22000の仕組みを活用して、ベテラン作業者の技術の継承やクレーム発生率の軽減などに積極的な取り組みを行っています。今回、認証取得の取り組みと、運用面の工夫点などについてお話を伺いました。
バニラ、ミルク、チョコレート、抹茶、ストロベリーなどおなじみの定番ミックスについて、乳脂肪分や原料によって、その甘さや香り、舌ざわりなどさまざまなソフトクリームのラインナップを揃えています。(写真中)
「CREMIA®」は、ソフトクリームを知り尽くした日世の技術の粋を集めて、真の美味しさを追求し、厳選された素材とこだわりの製法を駆使したプレミアムソフトです。(写真右)
顧客の要請をきっかけに新工場での内部統制強化にむけて認証取得に踏み切る
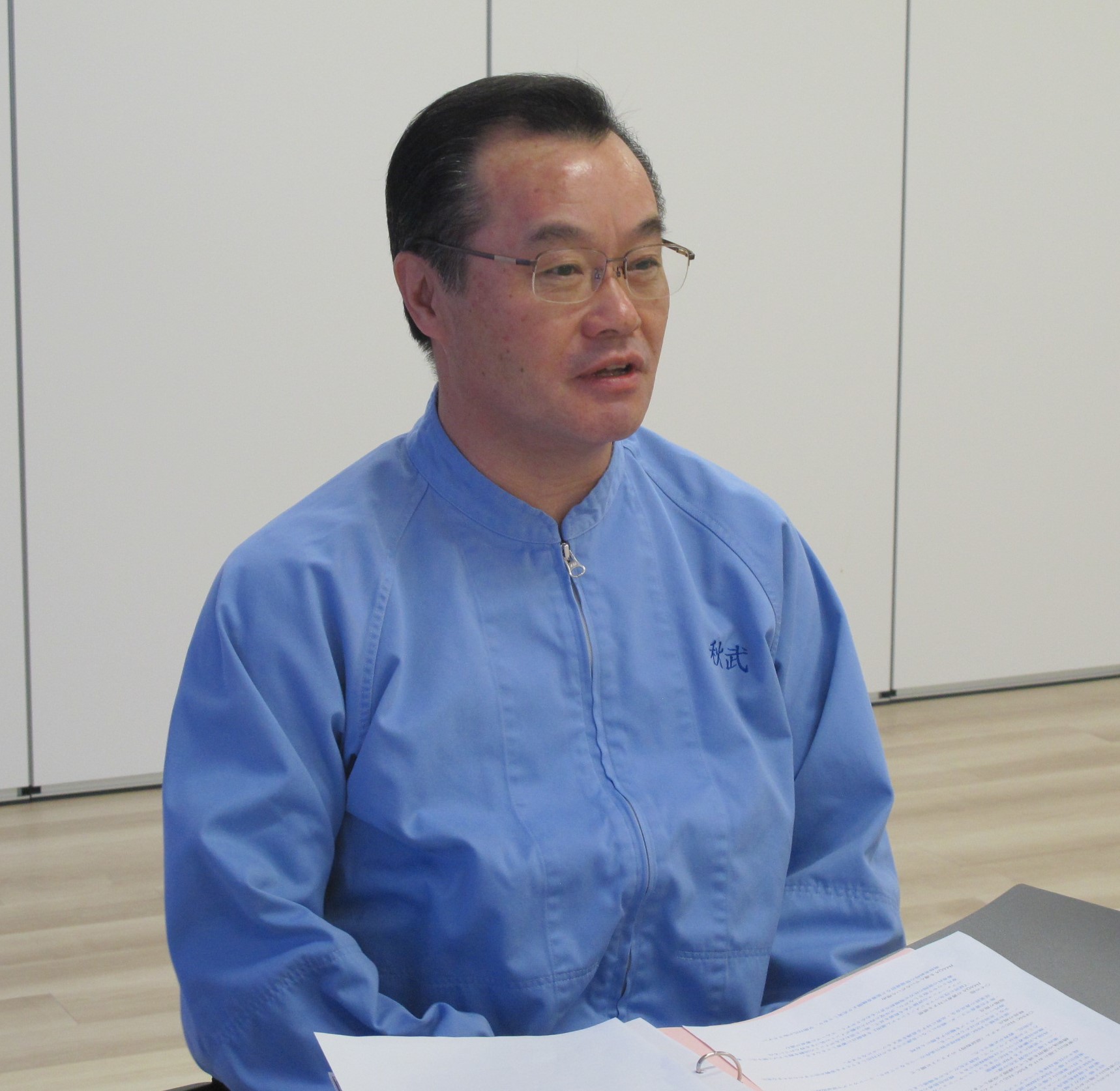
−FSSC22000を取得した経緯をお聞かせください。
秋武様:2008年にISO22000をモデルとしたマネジメントシステムを運用していましたが、当時は必ずしも認証登録は必要ではないと考えていました。
2013年になって、ユーザー(顧客)様から、FSSC22000認証取得を取引条件にする意向をお聞きし、当時は、大阪府の枚方工場と、神奈川県綾瀬市の東京工場の2カ所で製造を行っており、東松山工場への「移転統合プロジェクト」もすでに進行中でしたが、新工場での内部統制強化を図る目的で、まずは2014年に枚方工場で認証取得に踏み切りました。
−東松山工場でのFSSC22000に対応した仕組みを構築する上で苦心した点をお聞かせください。
秋武様:最初は、東京工場から移転をはじめました。東京工場の文化が根付きはじめたタイミングで、枚方工場を移転させました。この枚方工場の移転の際、退職者も出たことなどから、工場移転統合という大きなプロジェクトが進行している中、同時に、比較的少人数でのFSSC22000体制構築がテーマになりました。
金山様:「移転統合プロジェクト」では、コーンカップの焼成機・搬送ラインなどを旧工場より移設し、並行して新規焼成機の立ち上げが毎月1、2ライン立ち上げ作業がある中、「供給責任を果たしながら品質トラブルを起こさず、品質文化をいかに根付かせ熟成させていくか」といったことを最優先に考えて取り組みました。
新工場における食品安全の仕組みについては、旧枚方工場での文書をベースに構築しましたが、ユーティリティ設備は刷新されたことによるPRP再構築を行い、同時に仕事の仕方もよりよい方法に変えていく必要があったので手直ししました。また、外国人労働者が多く在籍している点も旧工場とは異なり、教育訓練における配慮も必要でした。
工場移転統合後のFSSC22000認証取得活動を通じて仕組みを改善
−つまり、ほぼ、新規に近い形からのスタートということでしょうか。東松山工場で新たな取り組みがあればご紹介ください
金山様:そうですね、ハード面が大きく変わっていますから、新規に近い形でしたね。東西の工場でコーンカップを製造していましたが、それぞれの工場ではメンバーの考え方や手順の細かい違いが数多くありました。また、東松山工場に移転統合するに伴って、人、設備面も大きく変わりました。
そこで、製造工程だけでなく、生産計画の立案から、メンテナンス、清掃など、工場における一通りの工程について、あらゆるリスクを洗い出し、出てきたリスクについて協議してコントロール方法の再確認とシステムの不足分があれば補強を進めていくことにしたのです。このリスク評価では、健康危害だけでなく、品質的な側面を対象にした「品質リスク評価」も踏まえて行っています。
ここで役立ったのが専用のツール(文書)です。このツールを通して、まず作業がどう行われているのか、東西工場で比較できるように把握し、その上で発展させていけるような課題の洗い出しを行いました。これらの課題の対応を検討することで、仕事のやり方の見直しにもつながっていきました。 両工場ともこれまでの経験に基づくよい取り組みを行っていたので、それらを融合させて発展することができました。
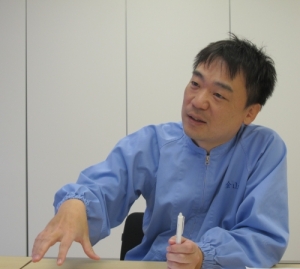
掲示物の工夫で外国人労働者にも分かりやすい教育を実施
−人の教育について工夫した点があればご紹介ください。
金山様:外国人労働者については旧工場ではわずかでしたが、現在は3割近くにも増えているので、外国人教育という大きな課題もありました。そこで、工場内の掲示物ひとつをとっても理解できるように、ひらがなやカタカナなどの表記をするほか、ベトナム語、中国語の3カ国対応の表示をしています。
また、外国人労働者にも分かりやすいように、手順書関係は文書マニュアルだけでなく動画マニュアルを活用しています。
他にも人の教育で工夫したことを挙げると、検品・箱詰めなどを担当する者は年間100人以上新規採用するので、一人前判定するツールとして、検品包装検定表(チェックリスト)を作成し、運用していることです。
こういったツールに基づいて学ぶと、一連の手順が効率的に習得できます。たとえば検定表で手順の統一と過去のクレーム対応の引き継ぎを行って、それらを周知しています。2018年からはiPadなどデジタルデバイスも導入して、これらの教育に活用しています。
効率的に習得電子ツールを活用した「従業員教育」「情報の一元管理」:品質管理課と製造課などの協働により、デジタルデバイスを使った「従業員の検品包装工程(電子帳票)の教育(写真)」「重要工程情報の一元管理」手法を新たに開発・運用しています。教育と情報の一元管理については、従来のやり方より大幅に効果的かつ効率的になっています。
秋武様:教育に関連しますが、旧工場では何も言わなくても業務ができていたのですが、実はそれが当たり前のことではなく、私たちが築き上げた文化の上に成り立っているのだという気づきがありました。当たり前のことを当たり前としないで、どう説明したらいいのかという学びのチャンスとなりました。
−品質文化を高めるために工夫されている点についてご紹介ください。
金山様:まず、食品安全チームメンバーによる定期会合や毎日の製造内容レビューは基本として徹底し、その上で、工場で働く全従業員がルールとその理由を理解して働くことが最も重要だと考えています。そのために、品質管理・衛生管理に関するルールとその理由を1日1テーマに1年分のネタを用意して「日めくりカレンダー」としてまとめて、朝礼で唱和しています。
カレンダーを作るにあたり、製造、保全、購買、生産管理、品質管理、庶務、開発など各職域から伝えたいネタを募集したところ、2週間足らずで1年分のネタが集まりました。この「日めくりカレンダー」は現場の意識を高める点で大いに役立っています。たとえば現場で新たな問題が発生した際、日めくりの朝礼ネタに追加しています。
この「日めくりカレンダー」については、「形骸化しないように自分たちの日々の仕事で出てきた問題点を加えていこう」という声が現場から寄せられており、作ってよかったと感じています。
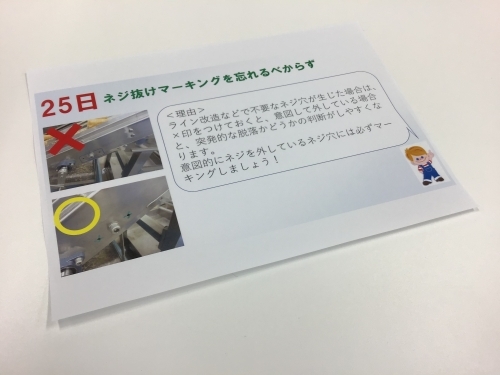
全員参加の「日めくりカレンダー」:品質や食品安全の基盤である従業員の意識を高め、風土を醸成するための施策のひとつとして「日めくりカレンダー」を従業員全員が参画しながら作成しています。このカレンダーはたとえば、現場の課題やお客様のお申し出内容、過去のトラブル事例などを盛り込んで注意を喚起しています。
独自のリスク評価方法を編み出しリスク対応のレベルを向上
−OPRPの管理手段でユニークな取り組みがあると聞きました。
金山様:コーンカップ搬送ラインは開放系のコンベアですので、搬送ライン上にある硬質プラスチック類の落下、混入リスクがあり、硬質プラスチックの管理をOPRPと設定しました。搬送ライン上の硬質プラスチックは数多くあり、すべて毎日点検することは物理的に不可能なため、点検箇所と点検頻度を決めるリスク評価方法を独自開発し、皆が納得した頻度で点検することができる体制にしました。
OPRP点検記録もどこを点検すべきかがわかるように、搬送ライン毎に点検必要箇所を写真にマーキングして誰でも点検できる工夫をしています。
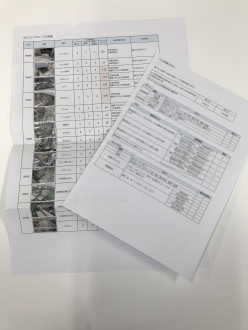
写真は硬質プラスチックリスク評価の一例。製品特性や顧客のニーズに対応するためにきめ細やかなリスク評価を実施することで、より効果的なリスク対応につなげています。
−食品防御、食品偽装予防で効果があった点をご紹介ください。
秋武様:東松山工場では55台の「品質保証カメラ」を工場内外に設置しました。現場は責任感と緊張感を持って、作業をすることができるようになっています。
当初のカメラ設置の目的は、食品防御、食品偽装予防のツールとしての導入ですが、現場トラブル発生時などは、製造された時刻までトレースすることによって原因追求が容易となり、再発防止策を講じるのに非常に役立っています。
お客様からのご指摘件数・発生率が2年間で1/3に減る
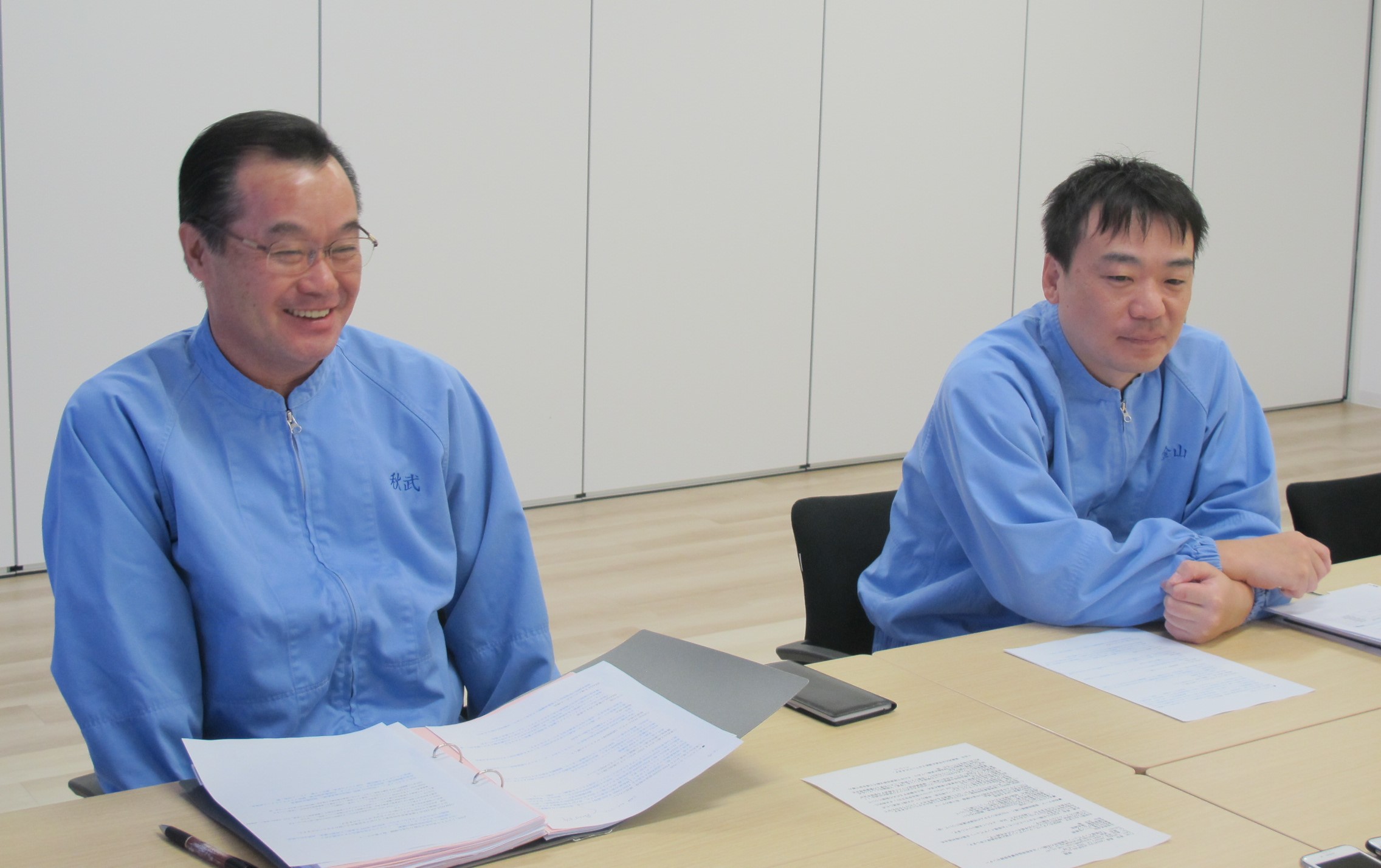
−仕組みの構築後のメリットをご紹介ください。
秋武様:まず、FSMSを運用することで業務改善が進み、品質・食品安全のパフォーマンス(お客様からのご指摘件数・発生率)が2017年比で2019年には約1/3まで大幅に減っており、過去20年間で最少となっています。まさに事業貢献につながっています。
これらの数字は現場の改善がなされた結果だと考えています。ここでは、たとえば文書に従って作業をするという基本的なしつけが大事だと思います。昔から、焼き菓子などは職人的な技能も必要とされていましたから、決められた手順や製造の規格範囲などをいかに守っていけるかが重要になってくるのです。
先ほど、私たちが当たり前だと思っていることが、実は一般の人には理解できなかったことに気づく機会になったとご紹介しましたが、メンバーが新しくなってきた中で、決められたことを徹底するこの仕組は有効だと感じています。
金山様:メリットを挙げると、現場で問題発生時は従来の表面的な対策では深く掘り下げずに処理していたところを、さらに深く掘り下げられるようになったことです。たとえば、原因と対策が一対一になるように、是正処置内容を見直すことや、個々の原因追求がしっかりできるようになったのです。不適合を放置せず、再発防止にかけるエネルギーが認証取得後は高まったと思います。第三者に説明責任を果たせるレベルにまで対処できていることもメリットだと考えています。
秋武様:コーンカップ業界では、FSSC22000を導入している企業が少ないですが、ユーザー様によるニーズが高まる中で、信用面でも効果が得られています。
海外からのお問い合わせもあり、輸出する際にも有効だと考えています。
経営に即したJMAQAの審査に共感
−日本能率協会審査登録センター(JMAQA)を審査機関として選んでいただいた理由はなんですか。
金山様:他の審査機関より規格改訂時の情報発信が速く、食品安全に関する研修セミナーなどが充実しているところです。企業サイドにとっては、情報をいち早くキャッチしたら、それらをすぐマネジメントシステムに取り入れられるメリットがあります。
実は第二者監査で外資系の審査機関ともやりとりがありますが、外資系の特性から、外国語用語を使った質問が多く、現場に戸惑いがありました。JMAQAの場合は、わかりやすい用語で質問や指摘をしてくれると期待しており、まさにその通りでした。
AI、IoT活用などいわゆるスマートファクトリー化を目指す
−最後に、今後の目標をお願いします。
金山様:これまでの泥臭い地道な改善活動も継続しつつ、AI、IoT、ITシステムを使ったスマートファクトリー化による品質・食品安全や効率面などでさらに上を目指すことです。そこで現在は情報デジタル分野のトレンドを採り入れたマネジメントシステムの運用を検討テーマにしています。投資対効果など経営のバランスを考えながら、取り組んでいきたいです。
秋武様:継続雇用が通例になっていく時代です。継続雇用のメンバーの活用が今後の課題となるでしょう。長年TPM活動を繰り広げてきていますがFSSC22000によってさらに高まってきており、提案改善活動も工場全体で活発に取り組んでいます。こうした組織全体の活動において経験者を活用することにより、さらなる技術の伝承を図っていきたいです。
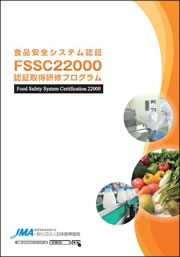
「FSSC22000 認証取得研修プログラム資料」
食品安全マネジメントシステム構築を支援
現在GFSI認証スキームの一つである“FSSC22000”が注目されています。 顧客からの要求を受け、認証取得に向け構築に取組む企業も多いなか、基幹となるISO22000やPRP要求事項のISO/TS22002-1規格要求項目に対して具体的にどの程度のレベルまで対応すべきか、悩んでいる推進者も少なくありません。 日本能率協会では、FSSC22000 認証取得研修プラグラムをご提供しています。
FSSC22000についての
お問い合わせはこちら
FSSC22000についての無料お見積り
FSSC22000についてのお問い合わせはこちら
食品安全認証・規格の認証取得事例について
食品安全認証・規格に関する取得事例インタビューを掲載しております。日本能率協会では、インタビュー内にもあるように、様々なニーズやお悩みに対して幅広くご提案をすることが可能です。
新規取得、切り替えをご検討中の企業担当様は是非ごらんください。