FSSC22000
(食品安全システム認証)
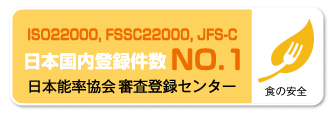
審査実績NO.1の審査期間だから安心!
審査および
認証取得支援サポート
CASE.1
【連載:効果的な運用事例 メリーチョコレートカムパニー様 [FSSC22000]】
安心安全な製品づくりが、社員一人ひとりの習慣になっていくことが理想
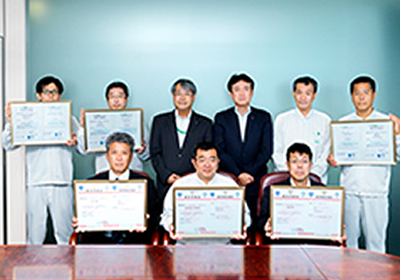
取材先:株式会社メリーチョコレートカムパニー
生産本部 生産推進統括部 統括部長 下田一人 様
執行役員 生産本部 大森工場長 市瀬信彦 様
生産本部 船橋工場長 柴崎義悦 様
生産本部 松戸工場長 中町博久 様 *所属役職等は取材当時のものです。
ロッテグループの一員としてギフト菓子の製造販売を行うメリーチョコレートカムパニーは、大森、船橋、松戸の3工場において、2017年8月24日、FSSC22000の認証を取得した。
認証取得の背景、システム構築や運用における工夫、成果や今後の期待について、事務局のリーダーを務めた生産推進統括部の下田一人氏と、3工場の工場長、市瀬信彦氏、柴崎義悦氏、中町博久氏にうかがった。
株式会社メリーチョコレートカムパニーの概要
本社所在地 | 東京都大田区大森西7-1-14 |
---|---|
設立(開設日) | 1950 年 |
従業員数 | 794 名 |
事業内容 | 高級チョコレートをはじめとするギフト菓子の製造、直販 https://www.mary.co.jp/mary/company/ https://www.mary.co.jp/mary/brandstory/ |
2016年3月 | 事務局立ち上げ |
---|---|
2016年6月 | キックオフ |
2017年4月 | 審査開始 松戸工場 第一段階審査 2017年4月20-21日 第二段階審査 2017年7月6-7日 登録 2017年8月24日 生産本部及び大森工場 第一段階審査 2017年5月24-25日 第二段階審査 2017年7月24-25日 登録 2017年8月24日 船橋工場 第一段階審査 2017年6月21-22日 第二段階審査 2017年8月3-4日 登録 2017年8月24日 |
【FSSC 認証取得の背景】高まる食品安全への要求を受けて、他社に先駆けて認証取得をめざす
2020年の東京五輪に向けてHACCPの義務化が進められるなど、食品安全に対する社会的な要求が高まっている。 メリーチョコレートカムパニーは、2016年6月に食品安全マネジメントシステム構築の取り組みをスタートし、わずか1年弱で第一次審査を開始、2017年8月には3工場でFSSC22000の認証を取得した。 まず、認証取得のきっかけについてうかがった。
「ロッテグループは、2018年3月までに株式会社ロッテの5工場で(浦和、狭山、九州、滋賀、戸田)でFSSC22000の認証取得を目標に掲げています。 当社の製品は大半が乾菓子なので食中毒などのクレームはありませんが、予防対策として食品安全マネジメントシステムを構築しておくことは重要だと考えました。また、FSSC22000は、ギフト菓子メーカーの取得が少ない規格であることから、他社に先駆けることで消費者や取引先に対するブランドイメージの向上につながり、様々な新規参入の機会が拡大することも視野に入れました」(下田一人統括部長)。
こうして同社は認証の取得に踏み切ったわけだが、短期間での認証取得がなぜ必要だったのだろうか。
それは、繁忙期を避け、現場に大きな負担を強いることなく食品安全マネジメントシステムを構築するためだった。また、短期間での認証取得が可能だったことにも理由があった。
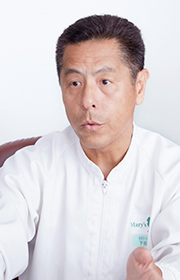
生産本部 生産推進統括部
統括部長 下田一人氏
「当社の主力製品であるチョコレートは、9月からバレンタインデーのある2月が繁忙期となるため、この期間内に審査を受けることは難しいと判断しました。
また、当社は2015年にISO9001の認証を取得しており、各工場長やスタッフとも相談した結果、ISO9001の仕組みを活かしながらHACCPプランを構築することで、短期間でのFSSC22000認証取得が可能であるという結論に達しました。
そこで、繁忙期となる前の2017年8月までの認証取得を目指して、2016年3月に生産技術部の3名で事務局を立ち上げ、6月にキックオフを宣言し、大森、船橋、松戸の各工場で食品安全チームを編成しました。
食品安全チームは、工場長がトップマネジメント、工場の部長が食品安全チームリーダー、課長や係長がメンバーを務めます。もともと私は営業部門にいましたが、営業の要求に応える工場の底力を知っていたので、3工場で同時に垂直立上げを行うことはできるという確信がありました」(下田一人統括部長)。
【システム構築の工夫ポイント】要求事項を現場に落とし込むために、「食品安全マニュアル」と「ルールブック」を作成
同社では短期間での認証取得に向けて、2016年4月には、日本能率協会によるギャップ分析を開始している。さらに6月のキックオフ宣言後には、コンサルティング会社によるHACCPプランの勉強会を月に1~2 回、定期的に実施するようになった。勉強会は各工場を巡回する形で開催され、これには各工場から合計30名程度の食品安全チームのメンバーが参加した。
「私たち生産技術部のメンバーは、HACCPプランの構築に必要な文書、例えばフローダイアグラム、ハザード分析シートなどをリスト化し、工場に作成スケジュールを通知するなど、現場とキャッチボールをしながら、認証取得までの活動が計画通りに進行するよう管理をしていました」(下田一人統括部長)。
認証取得をサポートする生産技術部が一番苦労したのは、食品安全マネジメントシステムISO22000と前提条件プログラムISO/TS22002-1の要求事項を、いかに現場に理解させるかということだった。 「ISO22000の要求事項を現場に落とし込むために、食品安全チームリーダーが、いつ、何をしなくてはならないか、どの部署が責任を持って行うのかを記載した『食品安全マニュアル』を作成・配布しました。また、前提条件プログラムISO/TS22002-1には、例えば、植栽の管理についての要求事項などもありますが、各工場にヒアリングを行い、年間の剪定回数、委託業者、管理部門、記録の方法などについての『ルールブック』を作成・配布しました。 『食品安全マニュアル』と『ルールブック』があることで、食品安全チームのメンバーは自分が何をすれば良いのかを理解でき、また役割分担もできるようになりました」(下田一人統括部長)。
【認証取得の工夫ポイント(1)】松戸、大森、船橋工場の順で、インフラ整備と審査受審を進行
同社では、松戸、大森、船橋の順に、1ヶ月程度の時間差を設けて審査受審を進めた。これは、各工場で操業開始時期が異なり、インフラの整備状況が異なるという問題を逆手にとって解決するためのアイデアだった。 「松戸は、2015年9月に竣工し、清潔区と普通区がきちんと分かれている最新の工場であり、一番認証を取得しやすい工場です。一方、一番古い船橋工場は、認証取得のためのインフラ整備に資金も時間も必要になります。そこで松戸工場の審査を最初に、その審査結果を大森工場、船橋工場に水平展開できるようにしたのです」 (下田一人統括部長)。
各工場では、それぞれ異なる課題を抱えながらも、他の工場の審査結果を共有するとともに、お互いの活動情報やノウハウを共有することで、抜け漏れのないようシステム構築を進めていった。
松戸工場は、工場も最新だが、ラインを動かすスタッフも若いことが課題だった。作業工程表であるフローダイアグラムの作成は、大森工場、船橋工場の力を借りながら、若いスタッフが苦労して進めていった。これは、実際にラインを動かす人たちの理解を深めなければ、たとえ認証を取得できたとしても、システムをきちんと運用していくことは難しいと考えたためだった。しかし、苦労したのは現場の若手だけではなかった。工場長は、こう振り返る。
「材料だけでなく、ラインで使用する機材や道具に対して証明を取らなくてはならない点で苦労しました。例えば、生産ラインでチョコレートにカバーリングする工程では、余分なチョコレートをエアで吹き落としますが、そのエアの安全性についても担保しなくてはならないのです」(中町博久工場長)。
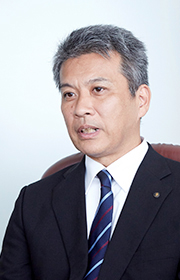
生産本部 松戸工場長
中町博久氏
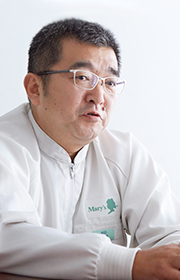
執行役員 生産本部
大森工場長 市瀬信彦氏
大森工場は本社部門もあるため、管理、企画、営業などの社員も出入りしている。そこで、製造部以外のスタッフにも、食品安全の意識付けを行うことが課題となった。 「全員が守らなければルールとして意味がないので、まず、ルールを明確にしました。清潔区、普通区を明確に区分けし、営業部を清潔区の外に出したり、シートシャッターで気密性を確保したりしました」(市瀬信彦工場長)。
そして船橋工場は、工場に物流部を併設していることが課題だった。工場が陰圧になり、物流部の倉庫から風が押し寄せて来るのだ。「空気はつながっているので、最初は、どこで空気の流れを切れば良いのかがわかりませんでした。今回、エアシャワーやエアカーテンを導入したことで、自分たちも空気の流れが理解できましたし、空気の安全も確保できました」(柴崎義悦工場長)。
【認証取得の工夫ポイント(2)】審査における指摘事項を全工場で共有
登録審査に向けて、同社では、コンサルティング会社による勉強会や模擬試験、「食品安全マニュアル」と「ルールブック」に基づいたシステムの構築と運用、インフラ整備に加え、生産技術部が予告なく工場を訪問して行う「抜き打ちテスト」など、万全の用意を整えてきた。また、3工場で各2回、全6回の審査についても生産技術部が記録を取り、指摘事項の共有化を図るといったフォローも奏功し、3工場とも2017年8月24日に登録の運びとなった。
日本能率協会を認証機関として選定した理由についてうかがった。「当社はISO9001の審査も日本能率協会にお願いしており、審査員の方々がISO22000の審査員の資格もお持ちで、当社について理解していただていることや、ISO9001でのフォロー体制も安心できるものでした」(下田一人統括部長)。
各工場の審査には、全工場の工場長と食品安全チームのメンバー、そして生産技術部が立ち会う形で行われた。実際に審査を受けた感想についてもうかがった。「松戸工場は最初だったので、基本的なことを審査されているという印象を持ちました。その後、大森、船橋と審査が進むにつれて質問がハイレベルになっていきました」(中町博久工場長)。
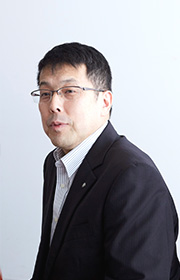
生産本部 船橋工場長
柴崎義悦氏
「二番手の大森工場では、松戸工場での指摘事項が短期間の間に是正されている点について、審査員の方々は好印象を持たれているようでした。また、審査と同時にアドバイスのような内容を直接のアドバイスではない形でいただくこともできました。悪いところだけでなく、良いところも指摘していただいたことに感謝をしています」(市瀬信彦工場長)。
「船橋工場は三番手であり、コンサルタント会社の勉強会や、生産技術部の抜き打ちテストがリハーサルのようになっていました。そのおかげか最終的な第一段階審査、第二段階審査では、変に構えることなく対応することができました」(柴崎義悦工場長)。
【認証取得の手応え、今後の抱負】FSSC22000 によってルールが確立され、時間短縮とコスト削減につながった
食品安全マネジメントシステムが構築されたことにより、同社では、「なれあい」が通用しなくなった。検査は済んだのか、安全の確認は取れているのか、製品テストに適合しているのか、こういったことについて文書でプロセスを追って食品安全チームに伝えるというルールが確立されたためである。
「ルールが明確になったので、工程の戻しの数が減って、効率化につながっています。それによって、コスト管理にもつながります。商品企画から始まって商品の生産を開始するまでのルートで、何をしなくてはならないかについて、誰もがわかるようになりました」(市瀬信彦工場長)。
「点と点が結びついて線になるのでなく、最初から線があって、そのルートの上をものが通っていくようになったのです」(下田一人統括部長)。
同社では、今回の認証取得にとどまらず、維持継続してくことが何よりも重要だと考えている。最後に約1年の間、認証チーム、会社を引っ張ってきたそれぞれの思いを語った。「認証を取得したことで、自分たちを含めた工場の全員が意識してやっていかなくてはならないと、気が引き締まりました」(市瀬信彦工場長)。
「安心安全のPDCA を、しっかり回せる工場にしていきたいと思います」(柴崎義悦工場長)。「まず、安心安全のレベルを上げていくことが大事です。それが、会社のブランドイメージの向上につながっていくと思っています」(中町博久工場長)。
「食事をするときに、このお箸は洗ってあるのかな、と思うことがありますよね。同じように、製品を作る一つ一つの道具にまで神経が行き届くようになっていってほしい。そうすると、これが仕組みではなく習慣になります。安心安全な製品づくりが、習慣になっていくことが理想です」(下田一人統括部長)。
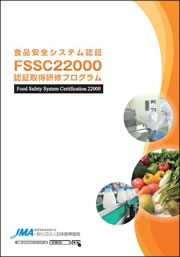
「FSSC22000 認証取得研修プログラム資料」
食品安全マネジメントシステム構築を支援
現在GFSI認証スキームの一つである“FSSC22000”が注目されています。 顧客からの要求を受け、認証取得に向け構築に取組む企業も多いなか、基幹となるISO22000やPRP要求事項のISO/TS22002-1規格要求項目に対して具体的にどの程度のレベルまで対応すべきか、悩んでいる推進者も少なくありません。 日本能率協会では、FSSC22000 認証取得研修プラグラムをご提供しています。
FSSC22000についての
お問い合わせはこちら
FSSC22000についての無料お見積り
FSSC22000についてのお問い合わせはこちら
食品安全認証・規格の認証取得事例について
食品安全認証・規格に関する取得事例インタビューを掲載しております。日本能率協会では、インタビュー内にもあるように、様々なニーズやお悩みに対して幅広くご提案をすることが可能です。
新規取得、切り替えをご検討中の企業担当様は是非ごらんください。